
ISO 9001 : 2015
CERTIFIED
Infrared Thermography
Infrared thermography is a technique of using a non-contact & non-destructive Infrared Scanning Camera to detect invisible Infrared thermal radiation of objects, and recording these pictures as thermal images called "Thermograms" to assist in identifying potential equipment failures.
Infrared thermography is a proactive troubleshooting and predictive maintenance tool. The test method uses an infrared imaging to detect, display and record thermal patterns and temperature across the surface of an object
Infrared thermography is a valuable tool for condition monitoring and preventive maintenance. Not only does it allow you to detect thermal abnormalities of machines, but it lets you do so in a non-intrusive, hands-off way while still getting results in real-time.
Advantages
-
Fault detection in electrical distribution networks.
-
Loose electrical connections
-
Overloaded circuits or phases
-
Deteriorated or damaged insulation
-
Valve failure in compressors.
-
Leaks of product from pipelines.
-
Misalignment of chain drives systems.
-
Bearing failure
-
Insufficient lubrication
-
Steam leaks
-
Faulty or loose drive belts.
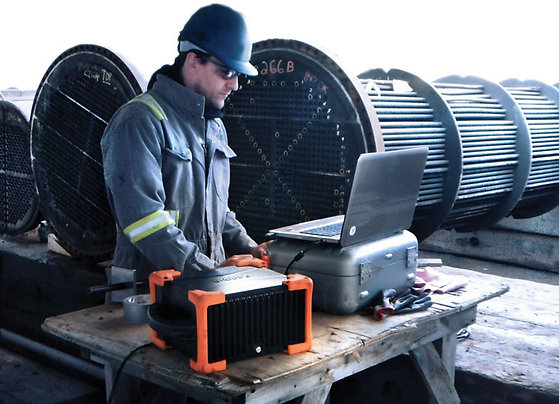
-
Rotary Kilns
-
Steam Turbine and Hydroelectric Generators
-
MCC & PCC Panel
-
Motor terminal connection
-
Mechanical Systems, Utilit
-
Switchyard
-
Valve leakage detection
-
Sinters, Gear boxes
-
High & Low voltage Electrical system
-
Refractory insulation inspection of Boiler, Blast Furnace, Kiln etc.